Page number |
Image No. |
Transcription
|
Thumbnail |
1 |
2 |
[2] Cover |
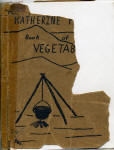 |
2 |
3 |
[Title page]
The Katherine Pettit Book of Vegetable Dyes
by
Wilmer Stone Viner
and
H.E. Scrope Viner
Cover Design by A.E. Viner
Saluda, N.C. The Excelsior Printers
1946 |
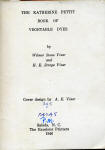 |
3 |
4 |
Copyright 1946 by
Mrs. Wilmer Stone Viner
Printed in the United States of America |
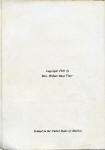 |
|
5 |
[Photograph of Katherine Pettit] |
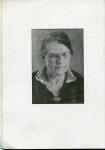 |
|
6 |
DEDICATION
In affection and gratitude this book of vegetable dyes is
dedicated to the memory of
Katherine Pettit
whose memorial tablet in the Pine Mountain School Chapel reads as
follows:
"Katherine Pettit, 1869-1936, pioneer and trail-breaker. Forty
years she spent creating opportunity for mountain children here and
elsewhere. In life, she ever refused praise. In death, she is too
great for it." |
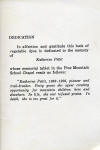 |
|
7 |
Table of Contents
Frontispiece
Katherine Pettit Dedication
Introduction _________________________ Page 11
General Remarks__________________________15
Washing and Mordanting the Wool ._ __________18
Dyeing _________________________________ 23
Red _______________________ 24
Yellow _____________________ 32
Blue _______________________ 46
Green ______________________ 57
Brown ______________________59
Black ______________________ 61
|
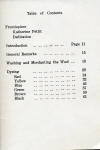 |
|
8 |
The Katherine Pettit Book
of Vegetable Dyes
INTRODUCTION
In almost all American families we find treasures of the past
that are carefully handed down from generation to generation, and
the one that is greatly treasured perhaps above all is the handwoven
coverlet with its lovely delicate colors mellowed by time. What a
history there is in these colors! In those bygone days you could not
go into the store and from a color card pick out just the dye you
wanted. The weaving by hand and coloring of these old coverlets was
no small task. And perhaps because it was such a slow, tedious task
is the reason why these treasures are so lasting and so dear to our
hearts.
There seems to be an awakening of renewed interest in natural
dyes throughout our country. Certainly there are no more beautiful
colors than can be gotten from our native trees, shrubs, and
flowers, and from the vegetable dyes that we import from other
countries. These treasured bits of weaving of the past, the colors
still bright, satisfying our eye with a peculiar beauty, surely are
the best proof of the lasting qualities of those dyes.
Nowadays interest has turned again to |
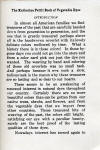 |
|
9 |
handmade things: you see more
handlooms in homes; and delight is taken in reproducing the
intricate patterns of the old coverlets. It seems fitting that the
wools which go into the making of these things should be dyed
according to receipts known to our grandmothers, usually handed down
by word of mouth.
Dyeing with vegetable dyes is an art for the individual
craftsman, for these dyes cannot be produced wholesale. In modern
dyeworks the wools are dyed in enormous quantities, and this
wholesale method is destructive to art and the personality of the
dyes themselves. So here is an opportunity for the amateur weaver to
get his own colors. He can with his own hands gather the roots and
bark and flowers, make up the dye himself, and then watch the color
grow in the wools.
And what a wealth of material lies ready for the gathering in our
woodlands and on our hillsides! Such are Sumac berries, Sedge grass,
Poke berries, the little wild Coreopsis that grows on our mountain
sides, Pine needles, sweet Laurel leaves, Walnut hulls, to mention
only a few. Formerly many additional sources of dye were expressly
cultivated - Madder in our flower gardens, and Indigo
in the Southen States. Now Madder must
12 |
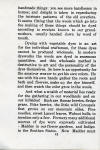 |
|
10 |
be imported from Europe and
Indigo from China or India, while tropical dyewoods like Fustic and
Logwood can, of course, only be obtained through importing houses.
When thinking over old receipts which have been used and passed
on from one generation to the next, it is interesting to note how
the chemist's science again and again confirms the use of one or
other ingredient for the use of which the old dyer can give no
reason beyond the fact of its accepted necessity.
For example, the old receipts for setting up the Blue Pot call
for home-made "Lye". Chemistry shows the active ingredient of this
extract to be Potash in a form most effective for the reduction of
Indigo. So, from his practical experience, the early dyer was led to
employ an essential chemical, obtainable in every household by
homely methods. In each colonial home the ash-hopper was a familiar
object, holding in store a crude ingredient of the soap kettle and
the dyepot.
Again, the formulas for the preparation of lichens for the dyepot
all spoke of the use of stale urine as a fundamental; and we now
know that its constituent, ammonia, is needed to free the active
principal, Orcin, and change it into Orcein, the essential coloring
agent. For us, probably, the use of the chemical is
13 |
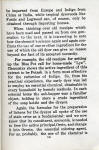 |
|
11 |
the easier method, but
undoubtedly the homely formula was the more practical for the people
among whom it originated.
Likewise in the old homely sayings, we find hidden scientific
truths:- "A bright pot for a bright dye and a dark pot for a dark
dye," this is literally true since in many vegetable dyes there is
tannic acid, which, combining with the inside of a black pot sets
free an oxide of iron which will sadden bright colors.
The old colonial method of getting variegated effects on warp and
filling was by tieing wrappings of corn shucks around the material
at intervals, protecting the chain in this manner by a waterproof
covering from the action of the dye when the material was placed in
the dyepot. The tied and dyed work of today is an echo of this.
|
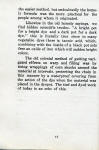 |
|
12 |
In the following pages will be
found receipts for preparing and using dyes from many natural
sources, including those just mentioned; however, there are a few
general hints which may help the dyer to obtain best results. If at
all possible, dye out of doors, as sunshine and air are most helpful
in obtaining bright colors. A Tripod can be erected of poles at very
little expense and the dyepot hung from this by means of a chain and
hook. Two pots should be kept for use, an iron one for dark and a
brass pot for bright colors. "Don't crowd the pot," is an old
saying, meaning you should allow plenty of water in all processes,
so that the wool may be easily moved about. Stir the pot often, so
that the dye may "take" evenly, and for the same reason, tie the
wool in loose hanks, not tightly, or there will be light places in
it, where the dye has not penetrated properly. Wool that has been
mordanted and then has dried should be again damped before putting
into the dyebath, to insure its taking up the dye evenly.
In using dye woods, berries, flowers, roots, etc., the materials
can be tied loosely in cheese-cloth bags, to save the trouble later
on of picking the bits out of the dyed wool; however, my experience
is that the color comes
15 |
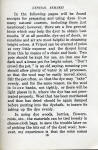 |
|
13 |
out more readily if the
material is not so confined. Barks, roots, and hulls can be put into
the dyepot first, and the dye extracted by boiling1 before the
wool is put in; but when berries or flowers are the source of the
dye, they had best be put into the pot at the same time as the
mordanted wool, since prolonged boiling dulls the colors obtained
from these sources. This especially applies to ' 'dye-flower", also
to Madder, I find.
The time of year has a great effect on the results gotten when
using vegetable dyes. In the Springtime all dyes from bark ar6 weak,
because at that time the sap, rising in the tree, dilutes the
staining material in the bark which is the source of our dye. Again,
as flowers and berries g-et mature they yield a duller dye. On the
other hand, Sedge-grass gives its best maize color when it has been
first dried.
The clear, crisp days of autumn are the best days of the year in
which to get brilliant colors. The statement, "Vegetable dyes are
most temperamental", may sound rather fanciful, yet it is not
unusual for two persons to employ exactly the same formula in dyeing1,
and still each gel; a different shade of color! Many factors
influence the final result, and the more carefully each process is
carried out
16 |
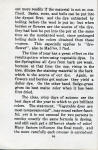 |
|
14 |
the more satisfactory will the
product be. The most important points to this end are:-
1. The cleanliness of the Wool.
2. The composition of the Water used;-its hardness or softness
will affect the quantities of dye or mordant required, and receipts
must be read with this in mind.
3. The Vessels in which the wool is dyed, -brass or copper for
bright colors and iron for sober ones, after the old saying: "A
bright pot for a bright dye, a dark pot for a dark dye.''
4. The length of Time in mordanting, which process must not be
hurried.
5. The Weather, - bright colors can be gotten most satisfactorily
on a bright day.
6. The Dyes themselves, - it can almost be said that vegetable
dyes give a slightly different color for each month of the year in
which they are gathered, e. g. green walnut hulls gathered in
September give a pinkish-brown, gathered in October the pinkish
shade is gone! |
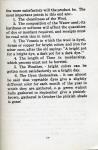 |
|
15 |
To prepare the wool for
mordanting is the first important step in dyeing with vegetable
dyes.
All wool, when it comes from the sheep, or even after it is spun,
is very dirty and oily. The best method to clean the wool is first
to make a thick lather with some good soap that has no lye in its
composition, rubbed up in hot soft water. When the wool is put into
the cleansing bath the water should be below boiling point and so
maintained, because if the temperature reaches that point, the wool
is liable to become "fleeced", that is, matted together. Immerse the
wool in several changes of water until all the heavy lanolin has
been washed out of it, and the wool is left light and fluffy. You
will find that some wool is yellow and cannot be gotten white. This
depends on the time of year that it is sheared; the Fall shearing is
always cream color, and no amount of washing will whiten it. Dry the
wool in the open air if possible; hang it where the air can blow
through it. When the wool is thoroughly dry, carefully wrap it up
and put away from dust and dirt till it is to be dyed.
MORDANTS
While there are a few vegetable dyes that
18 |
 |
|
16 |
WASHING and MORDANTING the
WOOL
impart permanent colors to wool directly immersed in them without
any intermediary process, and which are consequently known as
"substantive dyes", most of our vegetable dyes are fugitive unless
fixed by an additional chemical agent known as a Mordant,-from the
Latin word "mordere", to bite; such dyes are known as "adjective
dyes". The application of the mordant to the wool appears to enable
the dye to bite into its substance in a manner which it cannot do
unaided.
Mordants may be applied either previous to, along with, or after
the dye bath. My own preference is to their use before dyeing,
except in such cases as where the mordant is also a saddening agent;
e. g. Copperas, which chemical not only fixes fugitive colors but
also darkens their shade. The principal mordants that I use are:-
Alum, Muriate of Tin, Bichromate of Potash, and Copperas. Several
other chemical agents are used alone or with the foregoing, such as
Cream of Tartar. Lime and Lye are often spoken of as mordants, but
since their effect appears limited to varying the brilliance or
shade of the dye it would seem better, remembering our definition of
a mordant, to class them separately, as brightening agents. Let us
see how our mordants are used.
19 |
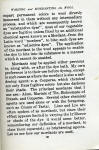 |
|
17 |
WASHING and MORDANTING the
WOOL
1. Alum. This is the most generally used of mordants. The best
results are gotten from alum in combination with cream of tartar:-
to one pound of wool use approximately four ounces of alum and
one-quarter ounce of cream of tartar. Too much alum would tend to
make the wool sticky. Heat the solution slowly, keeping just at the
boiling point; and don't neglect to make good the loss from
evaporation by frequently adding more water as the solution boils
away. The mordanting should go on for from a single period of one
hour to treatment extending over ten days, according to what shade
of color is wanted. For example, the best results were gotten when
mordanting for Mad-dar by boiling the wool in the solution for half
an hour each day for ten days consecutively, allowing the wool to
hang in a damp dark place between times.
2. Muriate of Tin. This is a most important mordant. By using
muriate of tin we get the most brilliant colors* It must, however,
be used with care and the proportions in the receipt not exceeded,
as its use tends to harden the wool, discoloring it slightly; used
too strong it renders it harsh and brittle. Its effect is enhanced
by addition of cream of tartar,- the proportions are, for one pound
wool, one-half
20 |
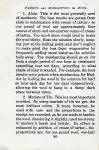 |
|
18 |
WASHING and MORDANTING the
WOOL
ounce muriate of tin and one ounce cream of tartar. Keep the
vessel covered, have plenty of hot water and boil slowly one hour.
3. Bichromate of Potash. This mordant is most satisfactory to
use, particularly in getting yellows. The proportions are:-Wool one
pound-, Bichromate of Potash one-half ounce. To mordant thoroughly,
boil for from one to two hours in a covered vessel.
4. Copperas. Both a mordant and saddening agent. Copperas is
employed by addition to the dye bath towards the end of the dyeing
process. Not only does it darken the color of the dyed wool, it also
renders it fast; and natural grey sheeps wool can be fixed by giving
it a bath of copperas. The receipt of the old homespun weavers is "a
pinch to the pot" and this suffices. Great care must be taken to
thoroughly cleanse the pots after they have held the copperas
solution, as the least trace of it will dull the colors and spoil
the brilliancy of madder, indigo, fustic, etc.
5. Vinegar. Both a mordant and brightening agent. I only employ
vinegar when working for a rose dye from Poke berries. These give a
brown dye that is fugitive, but by immersing the wool, either before
or after
the dye bath, in a strong solution of vinegar
21 |
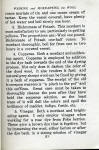 |
|
19 |
WASHING and MORDANTING the
WOOL
the brown color is transformed to a beautiful rose, and this
color is fast.
BRIGHTENING AGENTS
The use of Cream of Tartar has already been alluded to. Besides
this agent Lime and Lye have been employed as giving greater
brightness to dyes. In old text-books on Oriental vegetable dyes we
find a bath of lime water used before dyeing to add brilliancy to
the colors.
Lye that has been dripped from wood ashes is most valuable in
mordanting. Old soapmakers say that the best lye is made from oak
and hickory wood ashes. These should be put into a trough or hopper,
(an old bucket with a few nail holes punched in the bottom will do
well) and rainwater allowed to drip slowly through. These drippings
will be strongly impregnated with potash which used to form an
indispensable ingredient in the days when the country housewife made
her household soap. Immersing our dyed wool in a warm bath of water
to which enough lye has been added to make it taste biting will
brighten the colors, and, in the case of Dye-flower dye, it will
change the hue from yellow to a brilliant orange, almost a red.
22 |
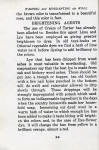 |
|
20 |
DYEING
I will now give the receipts which in practice I have found to be
the most satisfactory in producing the primary colors and those
which are derived from them. By this I do not imply that it is
necessary to mix dyes to get a hue that is not a primary color. On
the contrary I would discourage recourse to the mixing of dyes where
a single one of the shade wanted is available, believing that the
latter course gives a more permanent result. For example, orange is
not a primary color, but a mixture of red and yellow ;-it could be
gotten by first dyeing with madder and afterward dyeing the red wool
in a hickory-bark bath, but I would rather use a single bath of
Dye-flower, as likely to give more lastingly satisfactory results.
Let the dyer also recall what has been said under General Remarks as
to the factors affecting the final shade given by a dye,- he will
see that it is impossible to give a formula for an exact shade of
any color, and therefore, while the receipts which follow are
appropriate for the colors under which they are listed, taste and
skill can obtain an infinite variety of shade;- in this indeed lies
both the art and joy in working with Vegetable Dyes.
I would add that in practice pale shades of a color are less
satisfactory and less enduring than full ones.
23 |
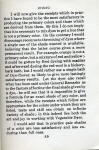 |
|
21 |
Madder. This is a
European plant cultivated nowadays in the Netherlands, France, and
the Levant. Its botanical name is Rubia Tinc-torum. It has a yellow
flower, however the root is the portion of tha plant of value to us,
as the dye is obtained from this, dried and pulverised. Madder was
grown in former days by the mountain people of the Appalachians to
furnish dye for their homespuns. The art of cultivating the plant
and extracting the dye was evidently brought originally by them from
England, but that practice has now died out. I have found plants of
wild madder in the overgrown corners of fields that have been long
neglected. These plants yield a true madder dye, but very limited in
quantity, making the use of wild madder impractical.
Madder contains two dyes, red and brown. Shades of red are
liberated up to the boiling point, after that the brown shades are
liberated and dull the red, hence in working for Rose colors it is
most important to keep the temperature below the boiling point.
When aiming at a compound color, as Madder and Old Fustic, dye
first in madder, remove the wool from the bath and put it into a
separate bath of fustic. This is necessary as
24 |
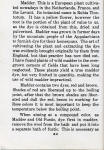 |
|
22 |
the
fustic requires to be boiled and the madder doesnot.
Thebrightestresultcan always begotten by adding Cream of Tartar to
the mordant.
It is better to start the wool in a cold or lukewarm dyebath and
raise the temperature gradually, to get the best color.
Brick Red.
Dissolve 4 oz Alum in 2 gals of hot water in a vessel with a
cover, put in one pound of wool and boil for two hours. Prepare
dyebath of 8 oz madder and sufficient water to well cover the wool.
Enter the mordanted wool into the cool dyebath, raise the
temperature slowly, keeping the wool moving constantly. Maintain the
heat just below boiling point for quite one and a half hours. Then
take out the wool, rinse thoroughly and dry it out of doors, hanging
it in the sun.
Crimson.
Dissolve 4 oz Alum and 1 oz Cream of Tartar in 2 gals of hot
water in a vessel with a cover, put in one pound of wool and boil
gently two hours. Prepare dyebath of 8 oz madder and sufficient
water to well cover the wool. Enter the mordanted wool into the cool
dyebath, raise the temperature slowly, keeping the wool moving
constantly. Maintain the heat just below boiling point for one hoar.
Then take out
2S |
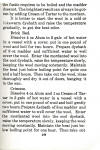 |
|
23 |
DYEING
the wool, rinse thoroughly and dry it out of doors, hanging it in
the sun.
Scarlet.
Dissolve 1-2 oz Muriate of Tin and 3-4 oz Cream of Tartar in 2
gals of hot water in a vessel with a cover, put in one pound of wool
and boil gently for two hours, being very careful to keep the vessel
covered. Prepare dyebath of 8 oz madder and sufficient water to well
cover the wool. Enter the mordanted wool into cool dyebath, raise
the temperature slowly, keeping the wool moving constantly. Maintain
the heat just below boiling point for half an hour. Then take out
the wool, rinse thoroughly and dry it out of doors, hanging it in
the sun.
Rosy Red from Madder.
Dissolve 4 oz Alum in 2 gals of hot water, put in one pound of
wool and boil for two hours. Take out the wool, put it in a bag and
hang it in a cool, damp place for ten days. Dampen the bag at
intervals with the alum water, in this way the wool becomes
thoroughly impregnated with the alum. Now prepare a dyebath of 8 oz
madder and sufficient water to well cover the wool. Enter the
mordanted wool into the cool dyebath, raise the temperature slowly,
keeping the wool moving constantly. Maintain the heat just below
boiling point for half an hour. Take
26 |
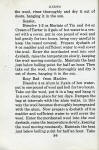 |
|
24 |
DYEING
out the wool, rinse thoroughly and dry it out of doors, hanging
it where the sun shines.
In all these receipts a variety of shades may be gotten by
varying the time that the wool is left in the dyebath, however the
paler shades are apt to be fugitive.
Cochineal.
Cochineal is a dyestuf f consisting of the dried bodies of female
insects found on the underside of leaves of several species of
cacti, native in Mexico and Central America. These cacti are
extensively cultivated for the purpose of raising the insects, which
are periodically gathered and killed by heat.
Cochineal when bought from the chemist sometimes looks silvery
and sometimes black. Either kind is equally good for dyeing, the
differing appearance being due to the mode in which the insects were
killed, those killed in stoves retain the natural white powdery
covering, and silver-grey cochineal results; when killed by steam or
hot water the insects lose this covering, and black cochineal is
produced.
Crimson from Cochineal.
Dissolve 21-2 oz Alum and 11-2 oz Cream of Tartar in 2 gals of
water in a vessel with a cover. Put in one pound of wool and boil
for two hours. Prepare dyebath of 1 oz cochineal in
27 |
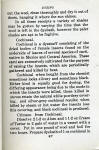 |
|
25 |
DYEING
two gallons of water. Enter the mordanted wool into the dyebath,
raise the temperature slowly, moving the wool constantly. Boil for
two hours. Take out, rinse, and dry the wool in the sun.
Scarlet from Cochineal.
Mordant the wool for two hours in a vessel with a cover, 1-2 oz
Muriate of Tin and 3-4 oz Cream of Tartar in two gals of water for
one pound wool. Be careful to keep vessel covered. Prepare dyebath
of 2 oz Cochineal in enough water to well cover the wool, enter the
wool when the dyebath is warm and raise gradually to the boiling
point. Boil for an hour, keeping wool moved about at intervals.
Remove wool, rinse it in clear water and dry in sunshine.
Kermes.
This dye is of the same nature as cochineal, that is to say. it
consists of the dried bodies of the female of certain scale insects,
which are parasites of several species of oak, especially an oak of
the Mediterranean region. They are round, about the size of a pea,
and contain coloring matter analagous to carmine. Kermes is still
used in Turkey, Morocco, etc; it is considered by most dyers to be
the best of all red dyes; Kermes was in use in Europe in the tenth
century and the old Gothic tapestries were dyed with it. These on
comparison with the later,
28 |
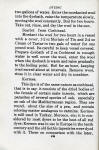 |
|
26 |
DYEING
Cochineal dyed tapestries prove its superiority both for shade
and permanence.
Red from Kermes.
Mordant the wool(l lb)with 3 oz Alum and 2 oz Cream of Tartar,
boiling it for two and a half hours. Take the wool out of the
mordant, wring out gently, saturate with "sour-water" (i. e., water
in which wheat bran has been allowed to ferment), put it into a bag
and leave it in a cool place for five days, moistening it
occasionally with the sour-water. Then dye in a bath of 10 oz Kermes
in 2 gallons of water.
Poke Weed. (Phytolacca Decandra.)
This is a coarse American perennial herb with racemose white
flowers and dark purple, juicy berries which latter yield a
beautiful rosy-red dye.
Rose-red from Pokeberries.
Mordant the wool with 2 gals water and half-gallon strong Vinegar
(for 1 Ib wool). Boil for one hour. Prepare dyebath with 2 gals of
the juice of ripe Pokeberries and 1-4 gal strong vinegar. Enter the
wool and simmer for one hour in a copper pot. Take out the wool and
let it drip a while. Dry in the sun. Afterwards wash and dry again
in the sun.
Sorrel. (Rumex Acedosa.)
A well known American wildflower. Its
29 |
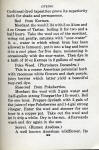 |
|
27 |
roots and stalks yield a
reddish dye.
Red from Sorrel.
Mordant the wool with Alum, 4 oz Alum in 2 gals water. Boil 1 Ib
wool in the mordant for two hours. Transfer the wool to the copper
dyepot, cover it with 2 gallons of water and to this add half a peck
of well-washed Sorrel, roots or stalks, in sufficient amount to make
a strong ooze. Boil slowly for one hour, take out the wool, rinse,
and dry in the sun. This will give a pale red.
Red Poppies, (genus Papava.)
A well known annual garden flower, the heads of which yield a
purplish red dye.
Red from Red Poppy.
Take a sufficiency of Red Poppy heads to make a strong ooze.
Mordant the wool with Alum (4 oz Alum in 2 gals water to 1 Ib wool)
for one hour, then transfer it to the ooze and dye at boiling point
for say a half-hour, or until the color satisfies. The best results
are gotten when the poppy heads are picked fresh and put at once to
use.
Other plants, and vegetable substances such as lichens, give red
dyes. The individual craftsman is urged to experiment with those
whose names follow here, this list has been gotten from various
sources, and there is a vast
30 |
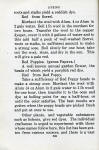 |
|
28 |
DYEING
field for research in trying out new mordants for many of them.
Birch. Fresh inner bark.
St. Johns Wort. Leaves
Wild Madder.
Red Root (Creanothus Am.).
Red Lobelia (L. Cardinalis).
Blood Root.
Red Oak. Bark.
Hemlock. Bark.
Potentil. Roots.
The Lichen, Ramalina Scopulorum.
The Lichen, Parmelia Omphalodes, or
"Black Crottle." The Lichen, Lecanora Tartarea, or Crotal.
31 |
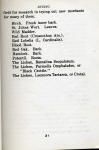 |
|
29 |
DYEING
YELLOW
Nature has supplied us so liberally with material for the Yellow
dye that we may well feel at a loss in making a choice. Hickory,
Black Oak, and Crab-apple Barks; Sedge Grass and Cockle Burrs;
Privet and Sweet Laurel Leaves; Marigold, Dye Flower, and Goldenrod,
all yield up their store of golden sunshine when suitably treated in
the dyepot.
They must all be subjected to the action of either Alum or acid
of some kind to properly impart their essence to the material to be
dyed, and just in proportion to the strength of the acid used in the
mordant will be the fullness and richness of the resultant yellow
tones.
Mathew Atkinson in his "Family Director, 1844" remarks "among all
the materials af^ fording the color Yellow there is perhaps none
cheaper or better adapted to general use in dyeing than the Black
Oak bark, as it imparts, when properly applied, every variety of
shade, with all the richness of which the yellow dye is
susceptible."
Black Oak Bark(Quercus nigra). A species of Oak native to North
and Central America. The inner bark is the source of the dye, and,
powdered, is sold as "Quercitron", the active principle of this
powder is a yellow, crystalline
32 |
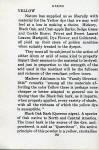 |
|
30 |
DYEING
substance Quercetin, which may be bought under the name
"Flavine". If it is desired to use the crude bark in dyeing some
care should be used in selecting the tree from which it is to be
stripped. A trial incision may be made in several trees and the one
whose inner bark appears most yellow chosen. The bark is best
stripped in May, and on removal it should be cleared of all outer
dead bark, retaining for use that part only which is soft and
growing. This should be carefully put away from dirt and damp in an
airy place until it is fully dried, then reduced to fine powder. It
will pulverise easily.
Yellow from Black Oak Bark.
Dissolve 4 oz Alum and 2 oz Cream of Tartar in 2 gallons of
water. Put in one pound of wool and boil for two hours. Prepare
dyebath of 4 oz powdered Black Oak Bark in 2 gallons of water,
transfer the mordanted wool (without rinsing) to the dyebath and
boil until the color appears of sufficient depth. Addition of a
small quantity of powdered chalk towards the end of boiling will
brighten the color.
Orange-yellow from Black Oak Bark.
In two gallons of water dissolve 2 oz Cream of Tartar and 1-2 oz
Muriate of Tin. Pat in one pound of wool, cover the vessel and boil
for one hour. Prepare dyebath of 4 oz powdered Black
33 |
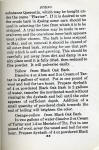 |
|
31 |
DYEING
Oak Bark in two gallons of water. Transfer the mordanted wool,
without rinsing, and boil until the desired color is obtained.
Old Fustic.
What Madder is among the red dyes Old Fustic is among the
yellows. Called Old Fustic to distinguish it from Fustet or Young
Fustic, the Cockspur Thorn, it is more often referred to simply as
Fustic. This dyewood is native to Mexico, Jamaica, and other
subtropical countries, its scientific name is Chlorophora Tinctoria
and it is a relative of the mulberry. It yields a bright yellow dye,
which is extracted from the heart-wood of the tree. The extract is
found to contain two coloring principles, Morin and Maclurin, they
both give yellow.
Yellow from Fustic.
Dissolve 1-2 oz Muriate of Tin and 3-4 oz Cream of Tartar in 2
gallons water in a covered vessel. Mordant one pound of wool in this
for half an hour, keeping vessel closed. Prepare a dyebath with from
2 to 6 oz of Fustic Chips, (according to depth of color desired).
Transfer the mordanted wool to the dyebath. Boil till color pleases,
but for an hour at least. Very long boiling tends to green it.
Old Gold from Fustic.
Mordant 1 Ib wool in 2 gallons water with
34 |
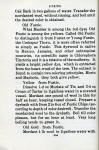 |
|
32 |
DYEING
1-2 oz Bichromate of Potash and 1-2 oz Cream of Tartar. Simmer
for an hour. Prepare dyebath of from 2 to 6 oz of Fustic Chips in 2
gals water. Transfer the mordanted wool to the dyebath and boil till
the shade desired is reached.
Lemon Yellow from Fustic.
Dissolve 4oz Alum and 1 oz Cream of Tartar in 2 gals water. Enter
1 Ib wool into this solution, simmer for 3 hours. Prepare dyebath of
4 to 6 oz Fustic Chips in 2 gals water. Boil for an hour to extract
the dye, then enter mordanted wool and boil slowly for one hour.
Sedge Grass (a plant of the genus Carex).
This grass yields a clear yellow dye. For this purpose it is best
gathered after it has become dry in the autumn. It is then easily
found, as it grows freely over unimproved pasture land and its
erect, strawcolored stems are left untouched by the grazing cattle.
Bright Yellow from Sedge Grass.
Dissolve 1-2 oz Muriate of Tin and 1-2 oz Cream of Tartar in a
covered vessel containing 2 gals water. Enter 1 Ib wool and simmer
slowly for 3 hours. Prepare dyebath of half a bushel Sedge Grass, or
enough to make a strong ooze, in 3 gals water. This ooze should be
of a clear, brownish color. Transfer the mordanted wool to this
dyebath and boil slowly for half an hour.
35 |
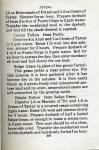 |
|
33 |
Golden Yellow from Sedge
Grass.
Dissolve 4 oz of Alum and 1-4 oz Cream of Tartar in 2 gals water.
In this mordant lib wool for 4 hours. Take vessel from fire and
allow to cool without removing wool. Prepare dyebath of 3 or 4 gals
water and enough Sedge Grass to make a strong ooze. After wool has
become cold in the mordant transfer it to sedge-grass dye-bath, and
simmer slowly until desired color is obtained; this is a beautiful
and lasting dye.
Old Gold from Sedge Grass.
Mordant the wool, using 1-2 oz Bichromate of Potash to 1 Ib wool
in 2 gals water. Simmer for one hour. Then transfer to a strong
ooze, j prepared as before and simmer till the desired shade is
reached. Rinse and hang in sun to dry; this applies to all Sedge
Grass receipts.
Maize from Sedge Grass,
Mordant 1 Ib wool with 4 oz Alum and sufficient water. Prepare
dyebath with 1-2 bu Sedge Grass. Enter mordanted wool; simmer twenty
minutes, or until a straw-like shade is obtained.
Hickory.
The bark of this well-known North American tree yields a yellow
dye. The inner bark contains the coloring matter and may be used for
dyeing at any time except spring, when the risingsap weakens its
efficacy for that purpose.
36 |
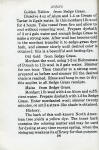 |
|
34 |
DYEING
Greenish-yellow from Hickory Bark.
For 1 Ib wool, dissolve 4 oz Alum in 2 gals water. Mordant for 4
hours, and allow the wool to cool in the liquid. Prepare a dyebath
of 1-2 bushel fresh inner bark of the Hickory. Boil the bark in 2
gals water until a strong ooze of a clear brownish-yellow color is
obtained. Transfer the mordanted wool to dyebath and boil for an
hour; then add a small quantity of hickory buds, continue boiling
for another half-hoar, rinse and hang in sun to dry.
Deep Yellow from Hickory Bark.
Mordant 1 Ib wool in 2 gals water in covered vessel with 1-2 oz
Bichromate of Potash and 1-2 oz Cream of Tartar for one hour.
Prepare dye-bath with sufficiency of hickory bark to make a very
strong ooze. Immerse the mordanted wool in this and boil until the
desired color is obtained. Pale shades with Hickory bark are not
lasting or satisfactory.
A still brighter yellow can be gotten with Muriate of'Tin and
Cream of Tartar as mordants.
Hickory Bark is often used to turn wool green after it has been
dyed with Indigo (see "Green").
"Dyeflower." A species of Coreopsis. A small, wild flower growing
freely on the hillsides in the Appalachians and adjacent country
37 |
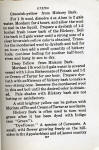 |
|
35 |
DYEING
side as far north as New Jersey. It blooms profusely all summer.
An extract from the blossoms gives a most beautiful yellow dye.
Golden-yellow from Dyeflower.
Mordant 1 Ib wool with 4 oz Alum and 1 oz Cream of Tartar in 2
gals of water for an hour. Prepare a dyebath of 2 gals water into
which a peck or so of dyeflower heads has been thrown. Transfer
mordanted wool to the cool dyebath and raise temperature quickly to
boiling point. Continue boiling till the desired color is gotten,
remembering that too prolonged boiling will dull the color.
Brilliant Yellow from Dyeflower.
Dissolve 1-2 oz Muriate of Tin and 1-2 oz Cream of Tartar in 2
gals water. In this mordant 1 Ib wool for half an hour, keeping
vessel covered mean while. Prepare dyebath of about a peck dyeflower
heads in 2 gals water. Transfer mordanted wool without rinsingto the
dyebath. Bring quickly to a boil and keep at boiling point until the
desired color is obtained. Prolonged boiling will dull the shades.
Deep Yellow from Dyeflower. Dissolve 1-2 oz Bichromate of Potash
in 2 gallons water. Into this mordant put 1 Ib wool and boil for two
hours being careful to keep the vessel covered. Prepare dyebath of
one peck of dye-
38 |
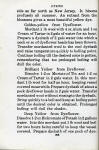 |
|
36 |
DYEING
flower heads in 2 gals water, put in mordanted wool, and boil for
twenty minutes, stirring constantly, and airing the wool at
intervals. Rinse and hang in the sun to dry.
Marigold (An Asteraceous plant of the genus Tagetes). Any of the
species gives a dye, but the African Marigold is the best to use in
the dyepot. The heads may be used freshly gathered or dry, but best
results are gotten with fresh ones. The color obtained with
Marigolds is especially beautiful, being exactly that of the
blossoms. It is also permanent, provided that the mordanting be
carried out thoroughly. During the dyeing process it is fascinating
to watch the transference of the color from the flowers to the wool.
On putting the blossoms into the dyepot and adding the mordanted
wool the golden color can be seen to leave the flowers and go into
the wool under our very eyes.
Marigold-yellow from Marigold.
Mordant 1 Ib wool in 2 gals water with 4 oz Alum and 2 oz Cream
of Tartar. Boil for two hours in covered vessel. Remove from fire
and allow wool to cool in mordant. Prepare dyebath of 2 gals water
and a peck or so of Marigold heads. Transfer mordanted wool to the
dyepot, which has been raised to the boiling point. Stir constantly
and air wool at interval. Continue
39 |
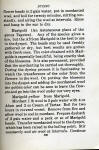 |
|
37 |
DYEING
only so long as necessary to get the desired color. Remove from
dyebath and dry in sun without rinsing. Later, rinse and again dry
in the sun.
Varying shades can be gotten with Marigolds by use of other
mordants in proportions already given.
Coreopsis (Coreopsis Tinctoria.)
A wellknown garden flower with yellow blooms. The heads may be
used for dyeing either gathered fresh in the summertime or may be
stored away for use in winter or spring.
Golden-yellow from Coreopsis.
Dissolve 1-2 oz Muriate of Tin and 2 03 Cream of Tartar in 2 gals
water. In this mordant 1 Ib wool for one hour keeping the vessel
covered. Prepare dyebath of 2 gals water and a peck or so of yellow
Coreopsis heads. Transfer mordanted wool, without rinsing, to
dyebath, which has been already raised to boiling point. Boil for
twenty minutes, airing wool occasionally. So soon as the color
pleases remove wool and, after rinsing, hang in the sun to dry.
Sometimes transferring the wool, after dyeing, to a bath of strong
suds made from a good quality of washing soap, and rinsing it
therein, will improve the color.
Various shades can be gotten with Coreopsis
4O |
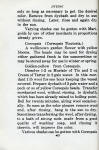 |
|
38 |
DYEING
by the use of other mordants, in the proportions already given.
Cockle Burr, or Agrimony.
A common weed with hairy stem, and small, inconspicuous, yellow
flower. The seeds are covered with little hooked spines and adhere
tenaciously to any rough-coated passerby. The leaves and stalk yield
a yellow dye.
Gold from Cockle Burr.
In 2 gals water make a weak solution of Bismuth, and in this
mordant the wool for an hour in a closed vessel. Transfer the wool
to a dyebath made up with 2 gals water and about a peck of fresh
leaves and stalks of the Cockle Burr. Boil until the desired color
is obtained. Then rinse, and hang in the sun to dry.
Privet (Ligustum Vulgare).
The leaves of this well-known oleaceous shrub yield a yellow dye.
Yellow from Privet Leaves.
Mordant 1 Ib wool with 3 oz Alum and 1 oz Cream of Tartar in 2
gals water for two hours. Prepare dyebath of 2 gals water and a peck
of Privet leaves, to which transfer mordanted wool, and boil until
the color pleases. This gives a good yellow.
Golden-Rod (Solidago).
There are many varieties of golden-rod,
41
|
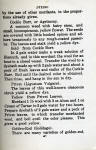 |
|
39 |
DYEING
dye may be gotten from the variety known as Dyers Weed,or Grey
Golden-rod (S.Nemoralis). Mordant 1 Ib wool with 4 oz Alum and 2 oz
Cream of Tartar in 2 gals water, boil for an hour, take out the wool
and hang in a bag in a cool place. Keep it so for ten days,
dampening it occasionally with the mordant. Then prepare a dyebath
of 2 gals water in which a peck or so of the heads and tender stalks
of Golden-rod have been boiled until a good stbng ooze is extracted.
Immerse the mordanted wool and boil till the desired color is
obtained. This gives a good, lively yellow.
Osage Orange (Toxylon Pomiferum).
An ornamental American moreaceous tree, allied to the Mulberry.
It was first found in the country of the Osage Indians, who employed
its wood to make bows and arrows, as well as to dye their war
bonnets, etc. The tree bears a yellow, apple-shaped fruit; it grows
in south Arkansas, Oklahoma, and Texas, and attains a height of 50
feet with a diameter of 2 feet. In the South-West an extract of the
roots and bark is made by boiling, and used as a dye. Like Fustic,
the heart wood contains two coloring principles, Morin and
Maclurin,and it has been urged that it be substituted for the former
wood for dyeing purposes; it is claimed to be a
42 |
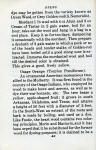 |
|
40 |
DYEING
faster dye than Fustic, cheaper, and a native product instead of
an import.
Osage Orange extract is marketed under the name "Aurantine". For
its use to produce various Yellow shades, the receipts given under
Fustic may be followed.
Crab Apple. The inner bark of this wild fruit tree yields a
yellow dye.
Yellow from Crab Apple.
Mordant 1 Ib wool in 2 gals water, in which has been dissolved 4
oz Alum and 1 oz Cream of Tartar. Boil for two hours. Prepare
dyebath of 2 gals water and enough crab-apple bark, freshly
stripped, to make a strong ooze. Transfer the mordanted wool to the
dyebath, and boil till the desired color is obtained.
Nettle. Plants of the genus Urtica.
The tops yield a yellow dye. Thorough mordanting is essential
with this, as with all yellow vegetable dyes.
Yellow from Nettles.
Mordant 1 Ib wool in 2 gals water with 4 oz Alum for two hours.
Prepare a dyebath with 2 gals water and a sufficiency of nettles to
make a strong ooze. Immerse the mordanted wool and boil until the
desired shade is obtained.
Sweet Leaf, Horse Sugar, or Dye Bush. (Symplocus Tinctoria.) In
early spring the
43 |
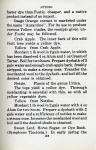 |
|
41 |
DYEING
bush of this name has clusters of intensely yellow, fragrant
flowers on the bare twigs, except in the deep South, where the
leaves remain on the tree all winter. These leaves are yellow-green,
bright, and have a silvery sheen. If dried the color becomes more
intense. The leaves are used to make a yellow dye. Yellow from Dye
Bush. Mordant 1 Ib wool with 1-2 oz Muriate of Tin and 2 oz Cream of
Tartar in a covered vessel for an hour. Have ready a peck of Dye
Bush leaves, and 2 gals of boiling water in the dyepot. Transfer
mordanted wool to the dyepot and add thereto the leaves. Boil for
three-quarters of an hour. Remove, rinse, and hang in sun to dry.
Other vegetable sources credited with yielding a yellow dye are
the following:
Willow. Leaves.
Hornbeam, or Ironwood. (Carpinus Beludus.)
Marsh Marigold.
Meadow Rue.
Buckthorn. Berries and bark (Rhomnus frangula.)
Barberry. Stems and roots.
Venetian Sumac, or Smoke Tree. (Extract, "Fustine".)
American Smoke Tree, or Chittam Wood.
Clematis. Leaves and branches.
|
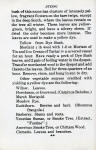 |
|
42 |
DYEING .
Ash. Fresh inner bark.
Sundew. (Drosera Rotundifolia.)
Lombardy Poplar. Leaves.
Pear. Leaves.
Plum. Leaves. .:
Tulip tree. Leaves.
St. Johns Wort. Flowers.
Ragweed.
Cynara. Artichoke.
Hops.
Rye.
Birch. Leaves.
Broom.
Tomato-vines.
Bog Myrtle.
Bramble.
Common Dock. Root.
Burdock.
Orange Root, or Golden Seal. (Hydrastis
Canadensis.)
Black Gum, or Tupelo. Bark. Spindle tree. (Euonymus Atropureus.)
Gorse. Bark, flowers, and young shoots. American or Kentucky Yellow
Wood.
(Cladrastis Lutea.) Pointed-Leaf Tick Trefoil. (Meibomia
Grandiflora.)
45 |
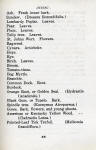 |
46 |
43 |
DYEING
BLUE
Indigo. This dye is the product of the plant Indigofera Tinctora,
largely cultivated in India, China, Guatamala, etc. For a time
Indigo was successfully grown in South Carolina and other southern
states, but has now entirely passed out of cultivation there.
The coloring matter does not exist as Indigo in the plant, but
develops when the freshly-cut plants are suitably treated. The
method employed is to throw them into vats of water, where they are
steeped for some time. The liquid is then drawn off into another
mixing vat, and there stirred till it assumes adeep purple color. It
is then left to stand until the sediment has been deposited. This is
afterwards removed, boiled, strained, and dried in a form suitable
for market. Usually it is sold in lump form, which is insoluble in
water, even when powdered, hence various means have to be employed
to fit Indigo for the dyebath.
To produce the best quality Indigo requires evidently a high
degree of skill.
There is an indigenous wild Indigo, (Bap-tesia Tinctoria) found
in the United States of America. It is a smooth, slender plant, with
deep grey-green leaves and small, pea-like
46 |
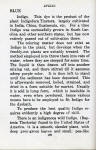 |
47 |
44 |
DYEING,
blossoms of pure yellow. This plant is to be found in great
abundance along the sides of the Appalachian Mountains; it may be
recognized by the peculiar property of its leaves, which turn black
on withering.
Preparation of dye material from Baptesia Tinctoria.
The Oldtime way of obtaining coloring matter from the Wild Indigo
was as follows: Pack the plant in a barrel and pour water over it.
Leave it to ferment, which it will probably do in a couple of days,
then squeeze out the plant and churn the liquor, then add lye from
oak-wood ashes until precipitation of dye occurs. To help this
result, bruise and soak some Red Sumac, and add the liquid from this
to the extract. When this becomes clear pour off the fluid and the
dye material will be found as sediment in the barrel.
To prepare Indigo for dyeing, three methods may be given: First,
the old-fashioned Indigo vat; second, Indigo Extract (Saxon Blue);
and last, the Soda-hydrosulphite vat. For setting up the Indigo vat,
or Blue Pot, many receipts exist. From these I have chosen a
mountain dyer's as follows: Place an iron kettle, capable of holding
at least five gallons, where it can be kept warm for several days,
as
47 |
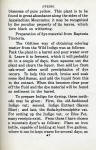 |
48 |
45 |
DYEING
on the hearthstone. Mix a pint of Madder with a pint of
wheat-bran, just moisten this, then put it at the bottom of the
kettle with a china plate over it. Now pour into the kettle two
gallons of warm water and one pint of lye dripped from wood ashes.
Tie 4 oz of good Indigo in a thick cloth, and suspend it in the
kettle. When it is soft, rub out the dye. If possible procure the
blue yeast from some other Blue-pot and add this to the kettle,
otherwise put in a cake of yeast.
Keep the vessel covered and warm, just luke warm, for four or
five days, when it will be ready for use. Experienced dyers can tell
when the dyepot is ready for the yarn by the smell of the solution.
This will be coated with a violet colored, lustrous film, and the
liquid, if poured from a spoon, will be clear, of a greenish-yellow
shade. Its condition for dyeing can be tested by dipping a small
hank of yarn, leaving it in a few minutes and then seeing if the
color has "taken" on the yarn at all. Shades from pale blue onward
can be gotten by repeated dipping and airing the yarn, remembering
that it is the oxidizing of the coloring matter in the air that sets
the color imparted in the pot.
For very dark blues it may be needful to
48 |
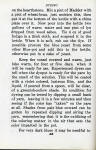 |
49 |
46 |
DYEING
leave the yarn in the pot for several hours, then air without
rinsing for a like period. The yarn should of course be thoroughly
washed when the right shade has been reached.
Saxon Blue.
To prepare the Indigo. Take a quarter pound of finely ground
Madras Indigo and one and a quarter pounds of strong Sulphuric acid.
Mix them well together in a deep earthenware or glass vessel of at
least one gallon capacity. When the Indigo is thoroughly
incorporated with the acid, stir in very slowly one-half ounce of
common salt. A thin, flat piece of wood can be used for stirring. Be
careful not to splash any of the mixture on the hands or clothes,
and this should be done out of doors or on an open porch, as strong
fumes are evolved. Continue to stir for at least five minutes, and
at intervals thereafter for at least an hour, covering the vessel
between times with paper or an old cloth. The mixture will at first
form a hot, bubbling mass, bat will settle down after a while. Set
aside in a dry place, and repeat the stirring at intervals during
the next three or four days. After this, if no more fumes are given
off, the dye is ready for use. It should be kept covered, and stored
in a dry cupboard, otherwise it will absorb moisture from the air,
|
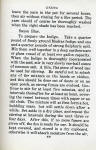 |
50 |
47 |
DYEING
and become weaker.
To Dye, Use a brass or enamel pot of about six quarts capacity.
Fill three-quarters full and place on the fire. With a wooden spoon
or spatula take out a half-teaspoonful of the dye (which should now
be in the form of a thin paste), add to the bath, and bring to
boiling point. The wool to be dyed should be at hand, already well
wetted in warm water. Take it up on a smooth stick, or long-handled
wooden spoon, and put it quickly into the dyebath. One or two hanks
may be entered at the same time, they must be moved about, to ensure
all parts being equally brought into contact with the dye. Lift and
air several times, continuing to heat the pot till it boils. After
boiling a few minutes lift the yarn and note the color as to shade
desired. With this process the color is taken up much more rapidly
and completely than it is with the Vat method, hence the need for
care in quickly getting the wool into the bath, and in contact with
the dye, to avoid uneven dyeing. When the liquid which runs from the
yarn as it is aired becomes nearly colorless the wool has reached as
dark a shade as that dyebath will produce. To get a darker shade,
remove the wool from dye bath whilst adding more dye,
50 |
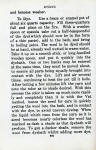 |
51 |
48 |
DYEING
stir this in well and quickly re-enter the yarn; this will ensure
an even color, free from streaks or light patches. When the yarn is
as dark as wanted, continue to boil for fifteen minutes. Rinse
thoroughly. A little Bicarbonate of Soda in the washing water
towards the last will neutralize any remaining acid in the wool.
Hydrosulphite-Soda Vat. This method is the most modern way of
dyeing with Indigo, it can be used either with the natural or
synthetic product. It produces a pleasing and fast blue. All shades,
from light to dark blue, can be gotten by varying the length of time
and number of dips that the wool is given in the dye vat. It does
require care in mixing and testing the solutions used, but,
given reasonable care, results can be depended on. The ingredients
are:
1 oz powdered Indigo.
1 oz Hydrosulphite of Soda.
1 & 1-2 oz Caustic Soda (Sodium Hydroxite). Apparatus needed
consists of a glass measuring vessel, graduated in ounces. A glass
stirring rod. A Hydrometer, such as is used for testing electric
storage batteries. A pasteurising thermometer.
51 |
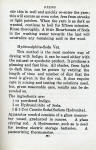 |
52 |
49 |
DYEING
To make the Stock Solution we must make two preliminary
solutions.
1. Into a glass or enamel vessel of sufficient size, measure six
ounces of tepid water. Gradually add to this the whole of the
Caustic Soda, stirring the while, and being careful not to splash
the liquid onto hands or face. It will heat considerably; set it
aside to cool.
2. Into a half-gallon pitcher, measure forty ounces of tepid
water. To this add gradually the Hydrosulphite, stirring the while.
Rub up the Indigo with a little warm water, making a thin paste. Now
check the Caustic Soda solution with the Hydrometer, it should read
between 1150 & 1200 on the scale (that is, it should be of
approximately 1.175 sp. gr.) Take three-and-a-half ounces of this
solution and stir it very slowly into the rubbed-up Indigo. When it
is thoroughly combined, measure off twenty-seven ounces of the
Hydrosulphite solution and stir it slowly into the Indigo and
Caustic Soda mixture. This is the Stock solution for dyeing; it
should be heated slowly to around 125 P., and left to stand for half
an hour, before use.
To set the vat. Use a brass or enamel vessel of three or four
gallons capacity. Fill three-quarters full of water at 125 deg. F.
52 |
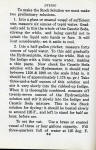 |
53 |
50 |
DYEING
Add to this three or four ounces of Solution No. 2 - this is to
de-oxygenate the bath. Let it stand for a quarter hour. Meanwhile
check the Stock Solution for correct condition, as follows: Dip the
glass stirring- rod and withdraw it. The liquid on it should be a
clear greenish yellow, changing quickly to blue. If the glass is
covered as it is withdrawn with blue patches, these indicate
undissolved Indigo, and call for addition of more of the No.2
solution (Hydrosulphite) - say two ounces.
On the other hand, a thick, milky appearance of the stock
solution calls for the addition of a little caustic soda solution.
In either case, if correction is needed, give the added chemical
time to function. However, given care in the first mixing and
measuring, the stock solution will probably need no additions.
To Dye. Measure off an ounce of the stock solution and stir it
into the dyebath, take care not to make many bubbles in so doing.
Set the dye pot over low heat and bring to 125 deg. F. Enter the
wool, previously wetted, move it around at intervals. After some
minutes lift the wool and note the color. It should be a
yellowish-green, changing on exposure to blue. Continue dyeing for
fifteen minutes, then lift and air for the same length of time. If
not
53 |
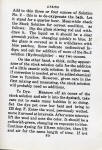 |
54 |
51 |
DYEING
dark enough, replace the wool in the dyebath, first adding a
little stock solution, and repeat the alternate dyeing and airing
until the color satisfies. Repeated immersions in the dyebath give a
better deep shade of blue than the use of a stronger bath will
produce. That is, the dyeing cannot be hurried, and still give the
best results. Remember to keep a watch on the temperature, this must
never exceed 140 deg. F., around 130 deg. F. is safe and effective.
Finally wash thoroughly, passing the wool through a weak solution of
sulphuric acid - a few drops to a gallon of water - during the
process, to neutralize any caustic left in it.
Simplified method for Blue with Hydro-suphite and Caustic Soda.
The chief danger in dyeing with the foregoing method is possible
damage to the wool by the caustic soda in the bath, too much will
make the bath feel slimy, and its effect is to reduce the wool to a
rubbery consistency. To preclude failure from this cause commercial
chemists have produced a sensitized tape, by which the strength of
the soda solution can be checked. This tape, called Phydrion Paper
(B), changes shade when dipped into the caustic soda bath, varying
with the strength of the solution, and its color can be compared to
a
54 |
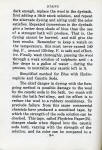 |
55 |
52 |
DYEING
scale shown on the little box in which the tape is put up. The
tape can be obtained from the Scientific Glass Apparatus Corporation
of Bloomfield, New Jersey.
To dye by this method, first boil up three to five gallons of
water in the dyepot. Continue boiling for half an hour, to drive off
all air held in suspension, then let the water cool to 120 deg. F.
Now slowly stir in caustic soda, a little at a time, dipping
fragments of the test tape at intervals, and comparing the shade to
the tints of the scale. When the reading is between 7 & 9 the
strength is correct. Now weigh out equal amounts of Indigo and
Hydro-sulphite, say one-half ounce of each. Rub the powdered Indigo
up with a little water, to make it mix easily and stir it into the
caustic soda bath. Then gradually stir in the Hydro-sulphite; let
stand ten minutes, gradually warming the bath to 125 deg. F. - not
over 140 F. Enter the wool, dye according to directions already
given for alternate dyeing and airing, etc. After washing, and an
acid bath to remove any remaining caustic soda, pass through a very
hot soapsud solution, using a mild soap, such as Ivory flakes for
this, then rinse and hang out to dry.
The resulting color by this method is a
55 |
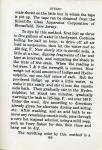 |
56 |
53 |
DYEING
very beautiful blue, and, because of its fastness, it should
always be employed when it constitutes the first step towards
producing green shades. In my opinion, however, it does not entirely
supercede the Saxon Blue method, as the shades of blue gotten by
that process have an unique charm of their own.
Slate Blue from Logwood.
Mordant one pound of wool in a covered vessel with half an ounce
of Bichromate of Potash, dissolved in sufficient water. Boil for an
hour, remove and rinse. While the wool is mordanting make a strong
ooze with Logwood chips in three gallons of water; strain out the
chips and add one-half ounce chalk. Enter the mordanted wool and
boil for an hour, at intervals raising and airing the wool. Then
wash and hang out to dry.
56 |
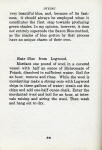 |
57 |
54 |
DYEING
GREEN.
Green is perhaps the least satisfactory of all vegetable dyes, so
far as fastness is concerned. To get a good green, dye the wool
first with Indigo, using preferably the Hydrosul-phite method. Then
put the blue yarn through an alum mordant, and green it in a yellow
dyebath. For this there is a large choice, - Old Fustic. Sedgegrass,
Hickory bark, etc.
The depth of color produced by the initial dyeing must depend on
the shade of green which the dyer desires as the final result of his
or her work. If a blue-green is wanted, then the yarn should be dyed
a deep blue first, and finished in a weak or normal yellow ooze. If
on the other hand a yellow-green is the objective, dye a pale or
medium blue, and finish in a strong yellow dyebath. Exact directions
cannot take the place of experience and judgment, the dyer must have
in mind just what she desires as the goal of her work, and persevere
to that end.
Green with Lily-of-the-Valley Leaves.
A fairly good green can be gotten from a few vegetable sources.
Young Lily-of-the-Valley leaves will give a delicate, fairly fast
green. For one pound of wool use four ounces of Alum, and mordant
for an hour. Prepare
57 |
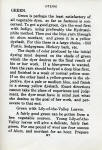 |
58 |
55 |
DYEING
the dyebath with a peck of young Lily-of-the-Valley leaves,
boiling them until they have colored the ooze. Transfer the wool to
the dyebath, without rinsing, and boil for an hour.
Bottle-Green with Logwood.
Mordant one pound of wool in a covered vessel with one-half ounce
of Bichromate of Potash for an hour. Remove and rinse.
Prepare a strong ooze with Logwood chips in three gallons of
water. Strain out the chips and add one-half ounce chalk to the
ooze. Enter the mordanted wool and boil for an hour, lifting and
airing it at intervals. The resulting color should be a dark slaty
blue. Rinse and transfer to a dyebath of Old Fustic. For this, make
up a strong ooze, either by boiling Old Fustic chips, or dissolving
the prepared crystals. Use a part of this to form the dyebath, of
medium strength; enter the dyed wool and boil for ten minutes; lift,
air, and rinse. Examine in the light for color. If not satisfactory,
add some of the Old Fustic ooze to the dye-bath, return the wool and
boil again. Continue this process till the color pleases. Boiling
time in the Old Fustic bath should total at least one-half hour.
58 |
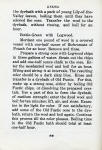 |
59 |
56 |
BROWN.
The most dependable source of our brown dye is the Black Walnut,
and wherever that tree flourishes the dyer will look to it for most
of the shades of brown which he or she has need for. Bark, roots,
and the hulls protecting the nuts are alike rich in the dyeing
material, but, since the black walnut is a valuable tree, we shall
not consider the use of either bark or roots, for equally good
results can be obtained from the hulls, an annual waste product at
the time of harvesting the nuts.
Brown from Walnut Hulls.
This is a substantive dye, and needs no mordant. Boil up half a
peck of hulls in three gallons of water, in an iron pot. Enter the
wool, moving it round till it is all equally wetted by the dye, and
boil for a length of time depending on the depth of color desired.
For a pale tan boil for a few minutes only; for darker shades
continue boiling for from ten minutes to an hour or more. This gives
a warm, rich brown, fast to light and washing.
To get a very dark brown add a pinch of copperas and a double
handful of sumac berries. Simmer the wool in this for an hour or
more and leave it in the ooze overnight. Then rinse very thoroughly,
both the wool and the
59 |
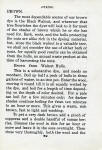 |
|
57 |
DYEING
dyepot before it is used for other work.
A pinkish brown can be gotten from the green hulls, when they are
first stripped from the nuts in the Fall. Hulls for later use must
be spread out and dried thoroughly before being bagged and hung up
for use througout the year.
Brown from Sumac.
Another shade of brown can be gotten with sumac berries alone,
gathered after they have turned red and boiled up in a brass or
enamel pot. This also is a pleasing shade of brown, with a greenish
tinge, and very fast. All depths of color, from tan to dark brown,
can be gotten, depending on strength of ooze and length of time for
which the wool is boiled therein.
Brown from Black Walnut Leaves.
In the fall a delicate shade of brown can be gotten as follows:
Gather a peck of Black Walnut leaves. Having cleaned the pot
thoroughly put a layer of these leaves in the bottom, then a layer
of wool yarn on these, then another layer of leaves, and so on
alternately. Pour in enough "fair water"to cover all. Then cover the
pot and set aside for about a week, after which time remove and
rinse the yarn. It will be found dyed a pleasing light shade of
brown.
6O |
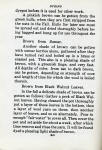 |
|
58 |
DYEING
BLACK.
A good black can be gotten from Walnut (either hulls, bark, or
root) in combination with Sumac. White Walnut gives the best
results.
Use the hulls to make a strong ooze, as when dyeing brown, but
put in a larger quantity in your iron pot, with three or four
gallons of water. Start a brisk fire under the pot and when it boils
add a double handful of sumac berries and a tablespoonful of
copperas. So soon as the last is dissolved enter the wool. Simmer
over a slow fire all day. Leave overnight in the dyepot and continue
simmering next day. The process should go on for at least
twenty-four hours in all. At the end of that time let the fire die
out, but leave the yarn in the dyepot until it has become cold. Then
remove and rinse the wool thoroughly. If the black is not
sufficiently intense, make up a fresh ooze and repeat the process as
detailed. Perseverance will produce a satisfactory black.
A quicker method of producing a good and lasting black is by the
double-dye method, using Indigo and Walnut. This was the way favored
by William Morris, who toward the end of the last century did so
much to keep
61 |
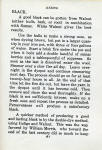 |
|
59 |
DYEING
handicrafts alive in England, when the industrial revolution
threatened their extinction.
Black with Indigo and Walnut.
Dye the wool first a deep blue, either by the Blue-pot or the
Hydrosulphite method. Rinse the blue yarn very throughly and then
transfer it to a dyebath containing a strong ooze already prepared
from walnut hulls, reinforced by a double handful of sumac berries.
In this dyebath boil the blue yarn for an hour or longer, then set
aside overnight to cool.
Next day take out the yarn, rinse well and examine in strong
daylight. If the color is a decided blue-black return to the walnut
dye-bath, add some more walnut hulls, and repeat boiling, with
addition of a pinch of copperas. Let the wool simmer for an hour or
so, then remove the dyepot from the fire and set aside to cool. When
it has become cold remove the yarn, rinse well and dry.
62 |
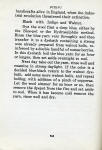 |
|
60 |
Here in this little book we
have put down a few receipts for dyeing wool. From this small
beginning the real dyer can go forward and have a grand time
experimenting, and get his own palette of colors with which to work.
Some will last forever, and some will fade gradually; the deeper and
richer the shade the more permanent the color always.
Not everyone is a dyer; some have success and some do not, but
any one will have an interesting time. For the colors Blue and Rose,
Indigo and Madder are the best. But for the other colors the woods,
the flower-gardens are ours to experiment with. There is dye in
roots, barks, flowers, hulls, leaves, and lichens, and many of these
dyes have never been discovered, nor the mordants with which they
are made fast. The dyer who has a real love of color and much
patience can work all this out for himself. We hope this book will
just be a beginning, and that you will go ahead and find many more
lovely colors. Anyway we know that is what Miss Pettit would wish!
63 |
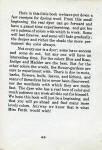 |
|
61 |
[Back cover] |
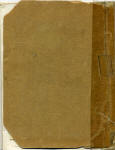 |